El objetivo era comprobar no solo la calidad de sus procesos, sino también las prestaciones de su ACE, el Centro de Experiencias para el Cliente, que se sitúa en el mismo complejo, y donde dichos clientes tienen la oportunidad de probar dinámicamente y comparar las transmisiones completamente automáticas de Allison en distintos vehículos.
Pero antes, un poco de historia
Allison Transmission es una compañía más que centenaria. Corría el año 1911 cuando James Allison formó parte de las personas que promovieron y construyeron el mítico circuito de velocidad de Indianápolis, donde competía con un equipo de carreras. Poco después estalló la primera gran guerra, y la ingeniería del equipo se destinó a la construcción de piezas para aviación. Una vez finalizada la contienda, Allison logró su primera victoria en las famosas 500 millas.
James Allison falleció una década después, en 1929, y la compañía que había creado fue adquirida por General Motors. Poco a poco fue evolucionando y, durante la segunda gran guerra, se especializó en la fabricación de transmisiones para vehículos pesados y de defensa (su actual ocupación). Así, en 1947 puso en el mercado la primera transmisión para buses y más tarde, en 1965, el primer modelo para camiones.
En 1947 puso en el mercado la primera transmisión para buses y en 1965 el primer modelo para camiones
Los siguientes hitos de la compañía son su fusión con Detroit Diesel en los años ’70, la consolidación con marca propia en 1987 y, en 2007, su salida de General Motors, continuando su camino en solitario. Fue en 2012 cuando comenzó a cotizar en la Bolsa de Nueva York. En la actualidad, está presente en 150 países y mantiene acuerdos de colaboración con más de 350 fabricantes de primeros equipos.
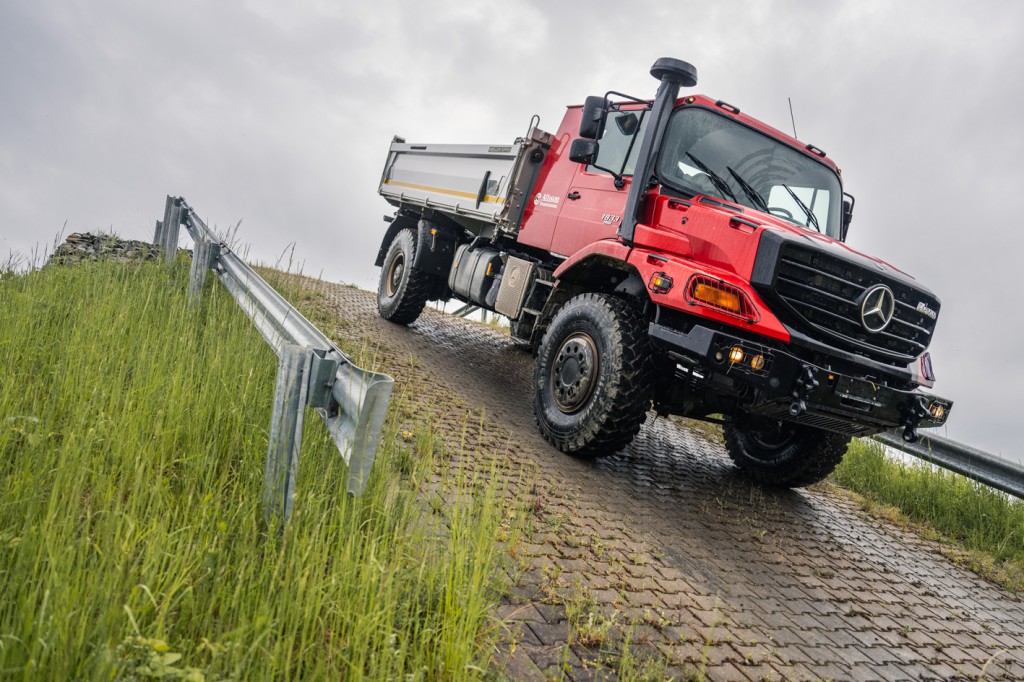
Esa relación con General Motors y Opel es la razón por la que Allison se instala en la mencionada localidad de Hungría, donde ya tenía presencia el fabricante alemán. En octubre del año 2000, comienza en sus instalaciones la producción de las transmisiones de la Serie 3000 y Torqmatic (esta segunda solo para buses), a las que se suma en 2005 la Serie 4000.
A partir de aquí, se aceleran los acontecimientos: en marzo de 2007 se fabrica la transmisión de Allison número cinco millones en todo el mundo, unidad que sale de Szentgotthárd; en abril 2008 se alcanza la cifra de 100.000 cajas en la planta húngara y, en octubre de 2011, tiene lugar la inauguración de las nuevas instalaciones (las que acabamos de conocer in situ) y la apertura en su interior de un Centro de Personalización de transmisiones, clave en el negocio de Allison. Para finalizar con las fechas, el pasado marzo se alcanzaron las 300.000 unidades fabricadas en Szentgotthárd.
La planta
Fue Peter Rezsnyak, el director de la planta, quien nos explicó todos sus secretos. Al menos, los que se puede contar. Sobre una superficie total de 106.000 metros cuadrados, cuenta con un edificio de 13.200 en el que acoge la línea de producción, el almacén, el Centro de Personalización y las oficinas, quedando el ACE justo a lado, a unos 200 metros.
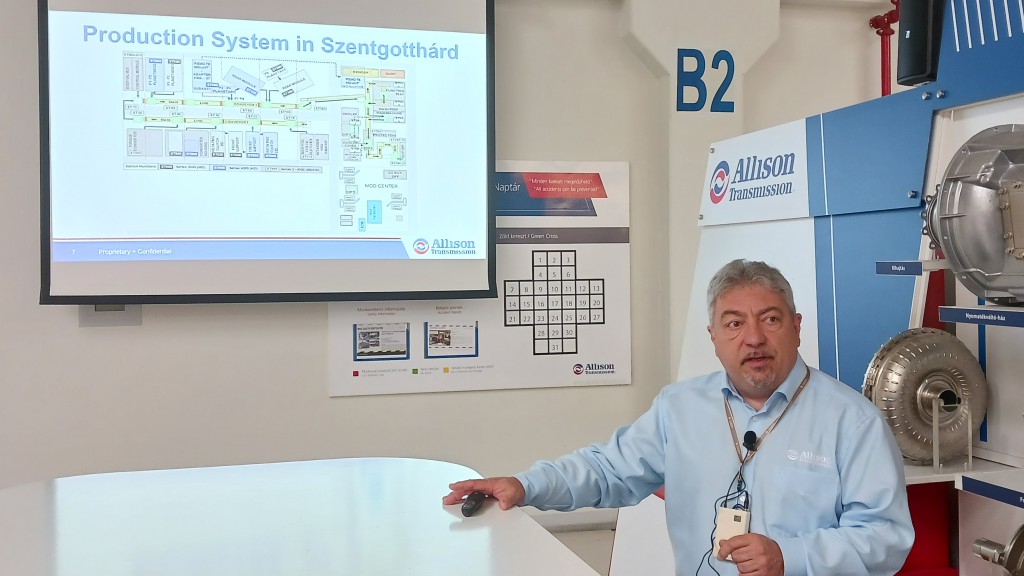
La nueva fábrica vio cómo se colocaba su primera piedra en septiembre de 2010, y apenas ocho meses después, tras trasladar de la anterior localización de Opel toda la maquinaria de la línea, comenzaba a operar. En la actualidad, los camiones que llegan a sus muelles salen cargados con unidades de las Series 3000, 4000 y Torqmatic, con destino a toda la parte del planeta que queda al Este de España, hasta Japón.
En Szentgotthárd cada persona está entre cinco o seis semanas en un puesto, antes de rotar a otro, y “la idea es que, aunque conozcan todo el proceso, estén 100% especializados en tres de estas estaciones como mínimo”.
Calidad y seguridad marcan el trabajo diario en la planta de Allison
La línea, que ocupa un total de 110 metros, consta de 16 estaciones y destaca, sobre todo, por sus “múltiples sistemas de calidad y seguridad”. En este apartado hizo Peter especial hincapié, mencionando que se controlan hasta 214 puntos y que, en caso de detectarse cualquier anomalía, la línea se detiene hasta que el operador la subsana. El control es periódico, tanto que “anualmente mandamos una transmisión de cada serie a Indianápolis, para que nos confirmen que todo va como tiene que ir”.
Otros sistemas que se utilizan para verificar el proceso es la inmersión en agua de cada unidad (para detectar burbujas que indiquen alguna fuga posterior), se analizan unidades de días anteriores para comprobar que siguen correctamente, y se repasan las superficies en busca de imperfecciones.
Peter va un poco más allá: “Si detectamos un fallo en una transmisión, con el número de serie buscamos las dos anteriores y posteriores, a fin de comprobar que no se ha repetido y es puntual. De no ser así, extendemos el rango a las 10 anteriores y posteriores, y así hasta que damos con el problema para poder subsanarlo. En ocasiones, tenemos que transmitírselo también a los proveedores, porque ellos son los responsables en origen”, aunque también reconoce que eso no suele suceder más de una o dos veces al año.
Mañana completaremos el reportaje con todo lo relacionado con el ACE y con las personas que nos acompañaron durante el viaje.